For over 72 years, Belzona polymeric technology has helped numerous asset owners across a myriad of industries to not only make seismic financial savings, but this technology has also enabled them to considerably mitigate their carbon footprints as well. This latter benefit is particularly paramount when considering the drive towards a net-zero by 2050 future for the planet, as outlined in the Paris Agreement.
At the COP28 Summit, negotiators from nearly 200 Parties came together in Dubai with a decision on the world’s first Global Stocktake. The Stocktake recognises the science that indicates global greenhouse gas emissions need to ‘be cut by 43% by 2030 compared to 2019 levels, in order to limit global warming to 1.5°C (2.7°F).’
However, the Stocktake notes that Parties are off track when it comes to meeting their Paris Agreement goals. As such, the Stocktake has called on Parties to take actions towards achieving, on a global scale, a ‘tripling of renewable energy capacity and doubling energy efficiency improvements by 2030.’
The Belzona Solution: a Circular Economic Business Model
Amongst the ever-growing arsenal of carbon mitigation technologies and initiatives, industrial coatings and repair composites can help numerous industries to significantly reduce their carbon footprints, in line with Paris Agreement targets.
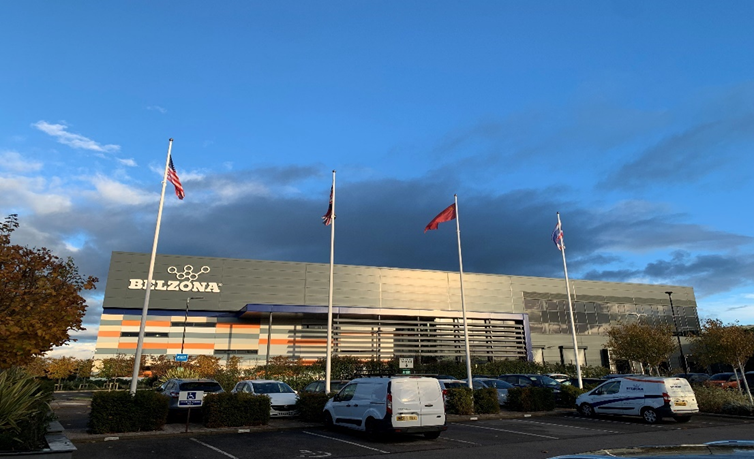
Figure 1. Established in 1952, Belzona is a global leader in polymeric technology
With a comprehensive range of polymeric systems such as epoxy repair composites, high-temperature coatings, liquid waterproof membranes, flexible roof coatings and pipe wraps, amongst others, these systems have been proven to not only repair and protect damaged assets across many different industries, but to also intrinsically improve them for the long term as well.
The environmental implications of this circular economic business model are astronomical. By bypassing the need to replace damaged assets and instead actively improving them, industries can make great strides in minimising their environmental impact.
In addition, by investing in these systems, this mitigates the fees that can accumulate in the process of asset replacement. These fees include: the cost of the asset being replaced, the labor required during the removal, disposal and installation process and also the downtime that can be incurred during this procedure.
For these reasons, an increase in investment into these technologies would help many different industries in the process of ratchetting up their 2030 emissions reduction plans, in line with the net-zero emissions by 2050 scenario, in a way that is also financially advantageous.
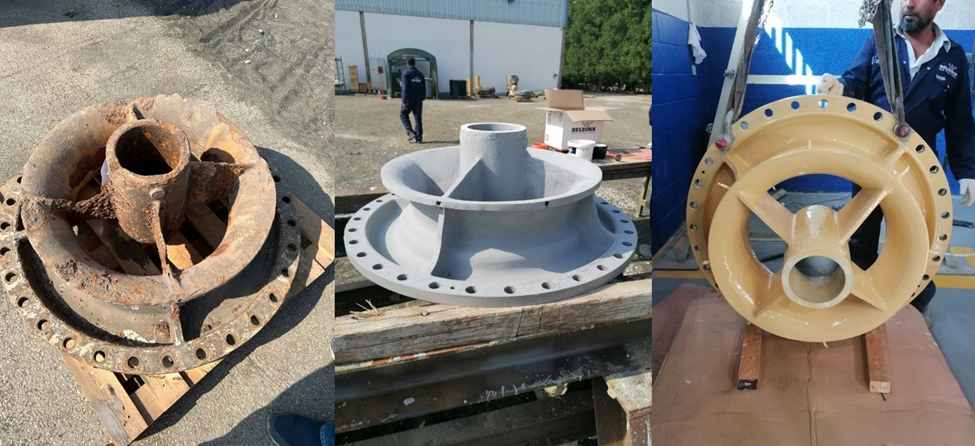
Figure 2. Corroded and eroded pump repaired and protected with Belzona 1111 (Super Metal) and Belzona 5821
Conventional Protective Coatings Won’t Survive
At the core of Belzona technology is polymer chemistry. In the Company’s laboratories located in Harrogate, UK and Miami, US, the Company designs, formulates, and manufactures a comprehensive range of polymeric solutions. These systems enable their industrial customers to repair and protect assets that would otherwise be damaged by aggressive service conditions.
For example, slurries and strong chemicals cause abrasion and corrosion as they pass down pipes and through production equipment. Factors such as these as well as elevated temperatures mean that conventional protective coatings won’t survive. As such, companies must turn to a high-performance polymer technology to protect their assets to an appropriate standard.
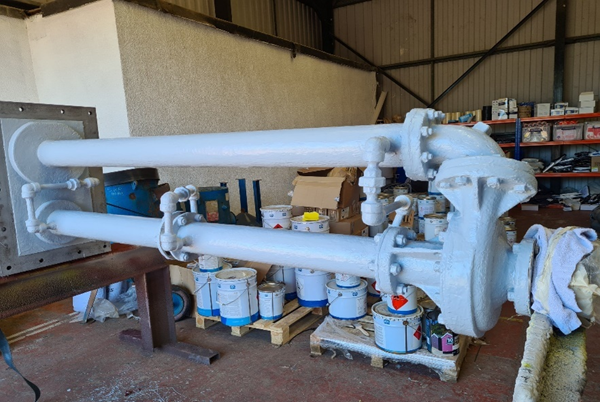
Figure 3. Pipes in Oil Refinery coated with Belzona 1593
The Evolution of Belzona
The Company was established in 1952. The Founder, Jorgan Svendsen, was fascinated with the mechanisms of corrosion, and how to repair, protect and improve assets against corrosion damage. Initially utilising a flame-spray method to protect fire extinguishers against corrosion, the Business moved away from hot work applications and developed a pioneering cold-applied, zinc-rich corrosion protection technology. This technology could be applied to a variety of steel structures. It worked by creating a polymer-zinc barrier that would resist aggressive corrosion and also protect the integrity of the steel beneath it.
Following on from this, Belzona then developed a range of polymer coatings and repair pastes. The original being Belzona 1111 (Super Metal), which has since been widely replicated over the years. This system was specifically designed for the repair and rebuilding of assets, before then coating and protecting them against any future damage. Applied onto damaged or worn surfaces in thick layers, these Belzona 1000 Series metallic pastes allow the substrate to be reshaped and reformed back to its original profile. The paste then sets, almost like the steel itself, and gives the original asset a new lease of life.
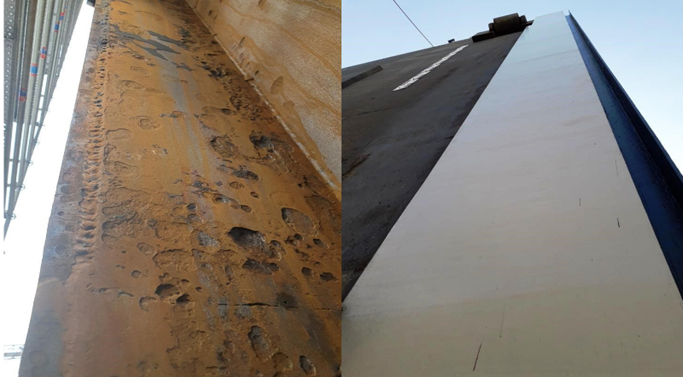
Figure 4. Damaged ship caisson repaired and protected with Belzona 1111 (Super Metal), Belzona 1331 and Belzona 5811 (Immersion Grade)
Since then, Belzona has gone on to develop a range of high temperature immersion linings. These are widely used in the oil and gas industry on structures that are subjected to water, steam, oil, sand, and aggressive chemicals throughout their processing life. Belzona has also developed composite repair systems made from densely woven structural fabrics made from glass fiber or carbon fiber, that can be used to return strength and fortify compromised pipes or other structures.
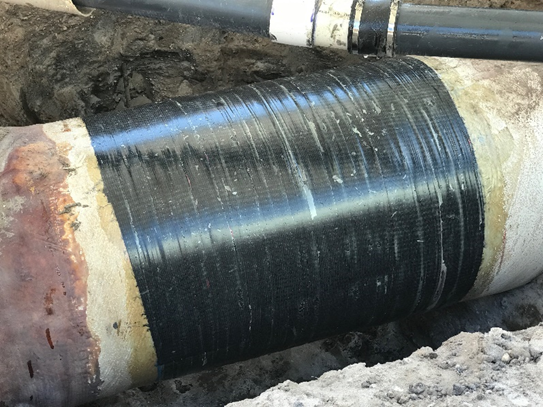
Figure 5. Desulfurisation unit rebuilt with Belzona 1511 (Super HT-Metal) and protected with high-temperature lining, Belzona 1593
The Company has found the composite repair method to be a rapidly growing market. For that niche, Belzona developed a brand called Belzona SuperWrap, now known as Belzona SuperWrap II. This system is comprised of a fluid-grade resin system and a bespoke hybrid reinforcement sheet, based on fibre glass and carbon fibre. The major benefit of the Belzona SuperWrap II system is its ability to re-instate/restore strength to the original substrate.
When a steel pipe is damaged or corroded, through chemical attack for example, then it will ultimately lose strength and can even leak. This can mean that entire plants or facilities will be shut down for lengthy periods of time. This is clearly a major issue as it could result in millions of dollars being lost every day. In addition, this system can be applied as a composite patch, pad or plate, bringing increased rigidity, corrosion resistance and chemical resistance to the asset.
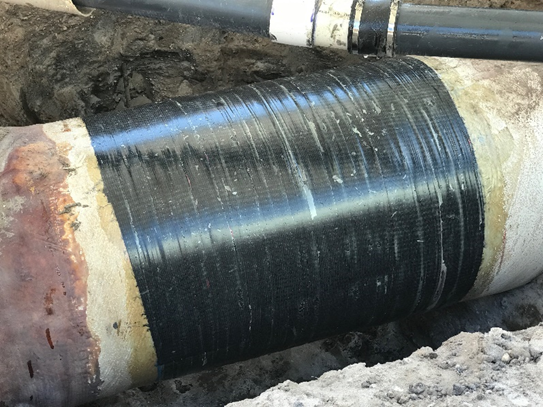
Figure 6. Pipe strength restored using Belzona SuperWrap II
Design, Develop, Manufacture
Belzona’s Chemists are involved at all stages, through design, development and manufacture. The Chemists work at the metaphorical drawing board, all the way through to supervising the first batch of a new polymer solution being made. As part of the development and manufacturing process, the Company focuses on sourcing materials that are commercially available, can provide the requisite performance, are of the highest quality, and which are as safe and sustainable as possible. By working with different chemical manufacturers, who create the building blocks of these solutions, the Chemists are able to apply their scientific knowledge and expertise, creating an easily appliable, safe, high-performance polymer product.
Testing is another key step in the development process. Belzona has fully equipped testing laboratories at their UK and US sites. These facilities allow the Company to study and characterise the performance of its products, and thereby optimise the formulations. Every solution undergoes an extensive programme of testing, the majority of which is carried out in-house. The testing is defined by the intended end-use for the product; for example, weathering testing for an exterior anti-corrosion coating or abrasion resistance testing for a slurry pump lining. It is Belzona’s investment in this testing capability which sets the Company apart from most competitors.
While the UK and US serve as the two core bases for Belzona’s global operations, the Company also has a global Network of 159 Distributors in over 120 countries. It also has corporate presences in the form of training and support centers in Thailand, Canada and China. Increasingly, Belzona is turning its attention to expanding its portfolio of sustainable solutions.
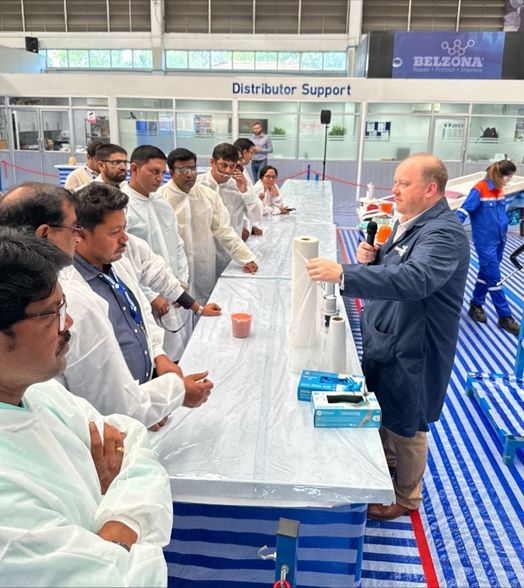
Figure 7. CEO, Barry Nisill, presenting Belzona solutions at Belzona’s Asia Pacific Office
Polymeric Solutions for a Sustainable Future
Repairing damaged assets instead of replacing them has always been fundamental to Belzona’s philosophy. This is encapsulated in the Company’s strapline ‘Polymeric Solutions for a Sustainable Future’. Originally, though, that philosophy was primarily driven by cost: it’s considerably cheaper to repair an asset than to buy a new one, so the asset owner can make significant financial savings.
For example, over the course of several years, a Steel Fabricator in the UK’s East Coast managed to save millions of pounds by deploying polymeric repair and protection systems onto more than 2,000 metres of its gas pipeline. This included epoxy repair mortars and stainless-steel protective coatings.
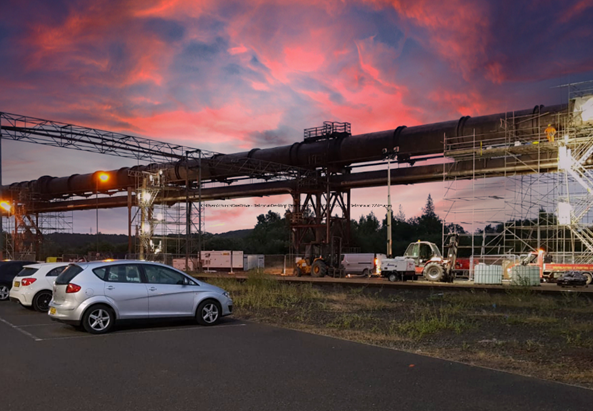
Figure 8. Steel Fabricator saved millions of pounds thanks to Belzona technology
To this day, this philosophy of repair instead of replace remains. However, the need for industries to reduce their environmental impacts is more pressing now than ever before. As such, Belzona polymeric repair materials and protective coatings have an important part to play in supporting this net-zero journey. They can help to reduce the carbon footprint across many different industries such as (amongst others):
Petrochemical, Oil and Gas:
Belzona has a wide range of epoxy-based metal repair composites and high temperature coatings and linings which have been used in the petrochemical and oil and gas industries since the late 1970s. These materials are specifically designed to provide outstanding erosion and corrosion protection, as well as chemical resistance for equipment operating offshore and onshore at various pressures and temperatures.
Belzona systems can be applied in the following areas within the petrochemical and oil and gas industries (amongst others): internal and external of process vessels, pipework, cold bonding, splash zones, storage tanks and secondary containment areas, carbon capture, decommissioning, fenders and hoses, heat exchangers, seawater filters and separator vessels.
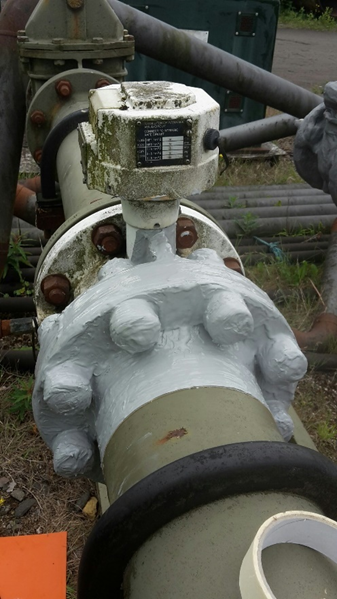
Figure 9. Flange protected against corrosion with flange encapsulation system, Belzona 3412
Marine:
Belzona's comprehensive range of cold-curing marine coatings and metal repair composites has been used by the marine industry for over 60 years. These products have been specifically designed to withstand harsh offshore conditions as well as provide exceptional resistance against erosion and corrosion.
Providing metal repair composites to shipyards around the world, long-term protection is proven by years of successful experience with ships and offshore structures. Manufactured according to the ISO 9001 quality management systems, Belzona materials are approved by classification societies from all around the world including: Lloyd's Register, American Bureau of Shipping, Bureau Veritas, RINA Services, DNV, China Classification Society and the Korean Register of Shipping.
Belzona systems can be applied in the following areas within the marine industry (amongst others): rudders, shafts, engines, shimming and chocking applications, rubber components, at sea repairs, storage tanks, exhausts, turbo blowers, stern tubes, auxiliary diesel engines, alternators/generators, tank cleaning systems, oily water separators, steering gears, pumps, heat exchangers, pipework, deck winches, lifeboats and access ladders.
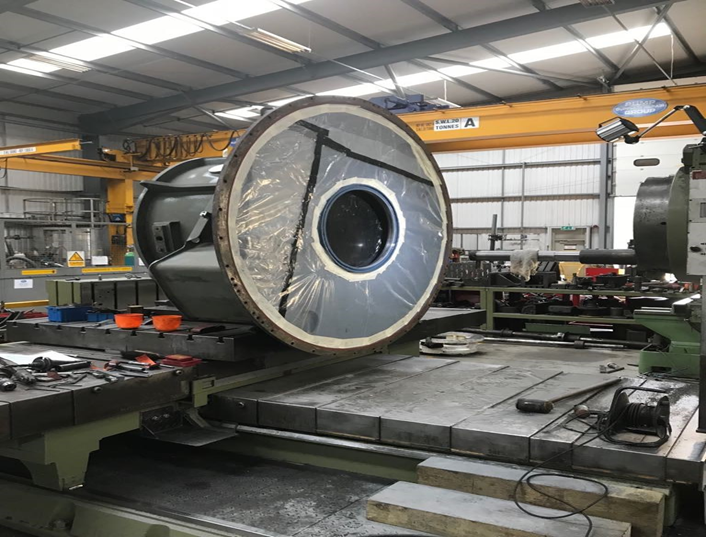
Figure 10. Voith Schneider propulsion unit built up with Belzona 1311 (Ceramic R-Metal) before being overcoated with Belzona 1321 (Ceramic S-Metal)
Mining and Quarrying:
Belzona's wide range of polymeric metal and rubber repair composites and durable protective coatings and linings have been used in the mining and quarrying industry for decades. These materials are specifically designed to provide outstanding erosion, corrosion and abrasion protection, as well as chemical resistance, for equipment operating in highly aggressive environments.
Belzona systems can be applied in the following areas within the mining and quarrying industry: solids handling equipment, fluid and gas handling equipment, mechanical equipment, chocking and shimming applications and facilities maintenance.
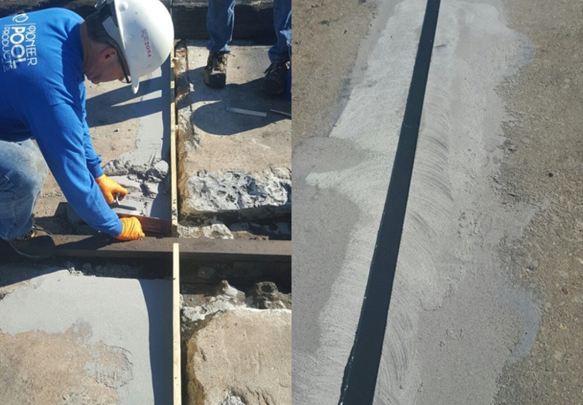
Figure 11. Expansion joint repair at Coal Mine using combination of Belzona systems
Steel:
From rolling mills to blast furnaces, critical equipment in the steel industry is susceptible to abrasion, erosion, corrosion and chemical attack. Belzona’s range of metal repair composites, erosion corrosion resistant coatings and durable linings have been engineered to meet the aggressive demands of this industry.
Belzona systems can be applied in the following areas within the steel industry (amongst others): fluid and gas handling equipment, solids handling equipment, storage tank and secondary containment areas, shimming of worn equipment and facilities maintenance.
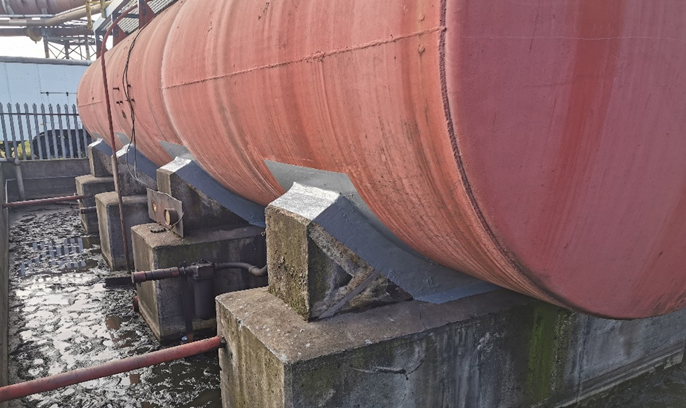
Figure 12. Tank and concrete saddles fortified with Belzona technology at Steel Production Site
Supporting Renewable Energy Industries
Not only can Belzona technology help to mitigate the carbon footprint across multiple industries, but these polymeric systems can also safeguard valuable assets within the renewables sector. For example:
Wind:
For both onshore and offshore environments, Belzona solutions for the wind power sector can help to repair and protect assets from these problems, whilst simultaneously making wind farm maintenance procedures more efficient and less time-consuming.
Belzona systems can be applied in the following areas within the wind industry (amongst others): blade restoration and leading edge protection (LEP), nacelle and generating components, rebuild solutions for mechanical components, turbine base and tower, damaged concrete, corrosion resistant encapsulation systems, corrosion and erosion protection for splash zones, surface-tolerant solutions for transformer leaks.
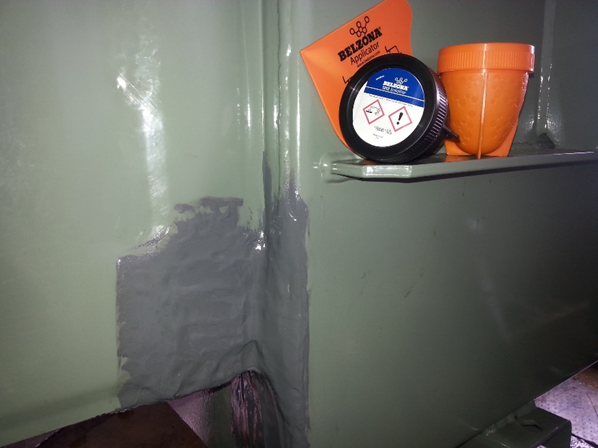
Figure 13. Emergency repair of leaking transformer at Wind Farm with Belzona 1212
Hydropower:
Within the hydropower industry, polymer technology can offer a plethora of benefits including resistance to cavitation, excellent resistance to erosion and corrosion and efficiency enhancement.
Belzona systems can be applied in the following areas within the hydropower industry (amongst others): Francis turbines, Kaplan turbines, wicket gates, inlet valves, switchgears and turbine casings, pipework, penstocks, dams/spillways and facilities maintenance.
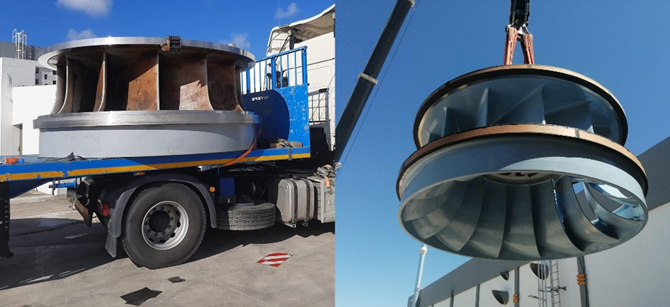
Figure 14. Corroded Francis turbine repaired with efficiency-enhancing coating, Belzona 1341 (Supermetalglide)
Biomass and Waste-to-Energy:
Belzona offers a wide range of epoxy-based repair composites and protective coatings to repair and protect biomass and waste-to-energy processing facilities and equipment from common problems occurring in the industry, including: abrasion, erosion, corrosion and chemical attack.
Belzona systems can be applied in the following areas within the biomass and waste-to-energy industry (amongst others): facilities maintenance, pipework, FGD units, chimneys and roofs.
Range of Systems to Repair, Protect and Improve
For each of these industries and application areas, Belzona has designed high-performance solutions spanning across five product ranges:
Belzona 1000 Series - for the repair and protection of machinery and equipment.
Belzona 2000 Series - for abrasion resistant linings and the repair and protection of flexible components.
Belzona 3000 Series - waterproofing systems for the repair and protection of buildings and structures.
Belzona 4000 Series - for the repair and protection of concrete subject to abrasion, impact, and chemical attack.
Belzona 5000 Series - for protection from physical, chemical, or bacterial attack in a diverse range of environments.
Belzona 6000 Series - Zinc rich epoxy materials for corrosion protection to steelwork.
Belzona 7000 Series – for structural bonding, shimming and chocking.
Sustainable Solutions
The focus on sustainability and conservation of the planet’s resources is informing much of Belzona’s future endeavors. For example, the Company has been supporting a UK-based Power Distribution Company and their customers whose assets are subject to SF6 leaks in their transformers. SF6 is described as the world’s worst greenhouse gas and is 23,500 times more potent than CO2.
In early 2022, Belzona created a tailor-made solution to stop leaks on a transformer owned by an electrical distribution operator. After several stages of prequalification, a trial repair was completed and has now been in service for several months. With Belzona’s support, the organisation is now achieving a 90-95% leak reduction rate, with an ambition to reach 100% in the near future.
The SF6 project reflects an increasingly important mission being adopted by Belzona: creating products that solve industrial problems in a safe and sustainable way.
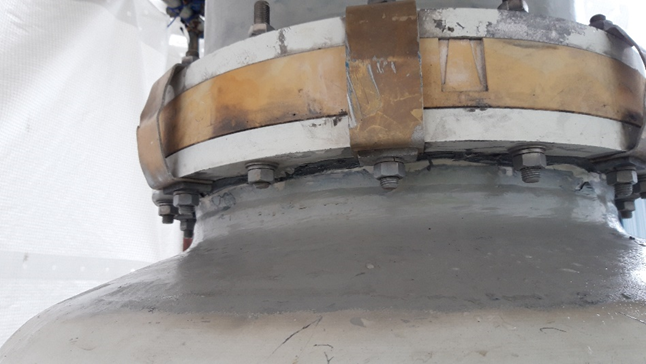
Figure 15. Belzona created a tailor-made solution to stop leaks on a transformer
Development of Products with High Levels of Renewable Carbon Content
Another important part of Belzona’s sustainability drive is its investigation into the efficacy of bio-based polymer solutions. One of the negative aspects of working with polymers is that the chemical building blocks used throughout the performance coatings sector are derived from oil - this means that an environmental impact is incurred.
However, Belzona has set out to address this challenge through its exploration and development of high-performance polymer solutions that use feed stocks derived from a renewable carbon source: plants. While bio-based chemicals have been available for low-performance solutions such as decorative paints for some time, the use of these types of chemicals has not previously been possible in the heavy industry market.
However, it is increasingly becoming apparent that chemical manufacturers are recognising the need for plant-derived polymers, in order to meet sustainability targets.
It is now possible to achieve very similar performance to oil-derived equivalents. Belzona is passionate about this ongoing change within the chemical industry. As a down-stream producer, the Company intends to work closely with manufacturers to encourage the adoption of more renewable-carbon solutions that don’t compromise on performance or quality.
Polymeric Systems: A Welcome Addition to the Arsenal of Carbon Mitigation Strategies
An increase in investment into industrial protective coatings and repair composites would help countries in the process of ratchetting up their 2030 emissions reduction plans, in order to achieve the net-zero emissions by 2050 target. Not only this, as discussed, these technologies are also instrumental in helping asset-owners across many different industries to make significant financial savings as well.
Indeed, Belzona recognises the critical role polymeric systems play in helping to support a more sustainable future for the planet in a way that is also financially advantageous. As such, they are committed to making ongoing investments into the development of polymeric systems that meet the ever-growing and changing demands of industries as they evolve towards a net-zero future.
About Belzona: Mission and Values
In April 2023, Belzona announced its new values – ‘Investment, Innovation, and Integrity’. These values are encapsulated in all five sectors of the Belzona philosophy - Corporate, Distributors, Consultants, Contractors, and Customers. These sectors work in harmony to provide the best products and services.
‘Investment’, the first of the new values, represents Belzona’s commitment to investing in its people, technology, and infrastructure. This includes investing in its employees’ training and development, as well as in the research and development of new and innovative products. Belzona’s focus on ‘Investment’ ensures that it stays ahead of the competition and continues to provide its customers with the best possible solutions.
Figure 16. Belzona invests in the ongoing training and development of its staff members
‘Innovation’ is the second value that Belzona has adopted. This value represents the Company’s commitment to continuous improvement and finding new and innovative solutions to its customers’ problems. For example, Belzona’s focus on ‘Innovation’ has led to the development of cutting-edge products, such as our range of high temperature linings.
The third and final value that Belzona has adopted is ‘integrity’. This value represents the Company’s commitment to honesty, transparency, and ethical behaviour. Belzona’s focus on ‘integrity’ ensures that it operates with the highest standards of conduct and maintains the trust and respect of its customers and partners. Strong work ethic and education across all areas ensures that the Business gets it, as best they can, right the first time from products to marketing, to technical support.
For more information, please visit: www.belzona.com